Sandblasting is a common method in metal fabrication and surface treatment. Before starting a powder coating project, it is typical for a company to use it to remove existing paint and aberrations from materials. While there are many other options for doing this, there are several key reasons why sandblasting is one of the most popular methods.
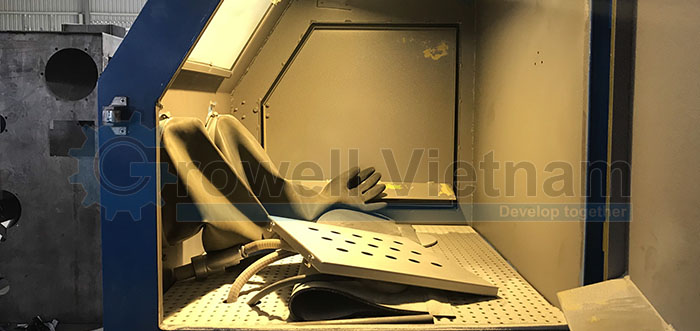
Flexible abrasives
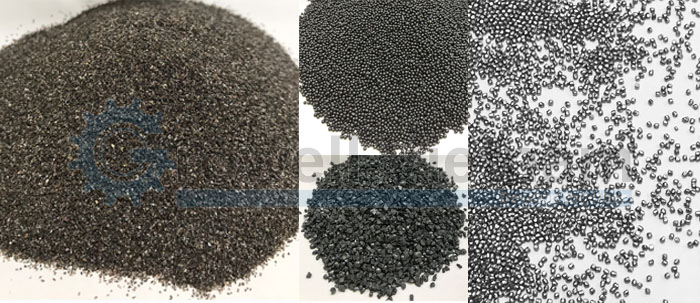
Even though it’s called sandblasting, you can actually use a lot of different abrasives media to clean metal. Abrasive media include steel shot, aluminum oxide, garnet, silicon carbide, glass beads or even organic particles such as walnut shells or corn cobs. Each type of abrasive has different applications and is suitable for different types of applications. Organic abrasives are a green choice because of their biodegradability, but cannot be roughened and reused many times.
Reuse abrasives many times
The sandblasting process allows you to reuse the abrasive to reduce costs. Each bead has a different reusability. Reusability of particles also depends on factors such as injection pressure, injection distance and injection angle. The greater the injection pressure, the more fragile the granules are, and the reusability is low. Sandblasting distance should be from 25 – 40 cm and at an angle of 30 – 45 degrees from the surface of the item to be sprayed
Convenient
When you try to remove paint or clean metal surfaces by hand, it is an extremely laborious process that takes a lot of time and effort. Sandblasting is a much more convenient solution, allowing for faster removal times with less effort on the part of the worker.
Perfect surface preparation method before coating
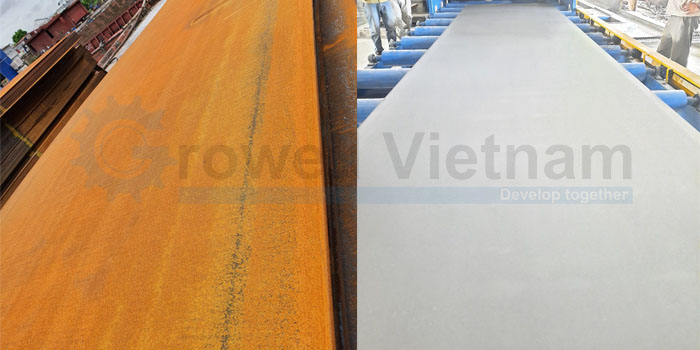
Even if you’re not painting metal surfaces, sandblasting can be a necessary first step in preparing for a paint job. Sandblasting is highly effective in removing old paint stuck on metal surfaces. Other paint removal methods that fail to remove the old paint will reduce the perfection of the new paint.